Home |
Michael Webb |
Building Statistics |
Thesis Abstract |
Technical Assignments |
Thesis Research |
Thesis Proposal |
Presentation |
Final Report |
Reflection |
Senior Thesis eStudio |
While great efforts have been taken to provide accurate and complete information on the pages of CPEP, please be aware that the information contained herewith is considered a work-in-progress for this thesis project. Modifications and changes related to the original building designs and construction methodologies for this senior thesis project are solely the interpretation of Michael Webb. Changes and discrepancies in no way imply that the original design contained errors or was flawed. Differing assumptions, code references, requirements, and methodologies have been incorporated into this thesis project; therefore, investigation results may vary from the original design.
|
|
 |
|

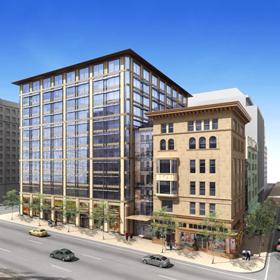 |
Rendering from the corner of 1199 F Street |
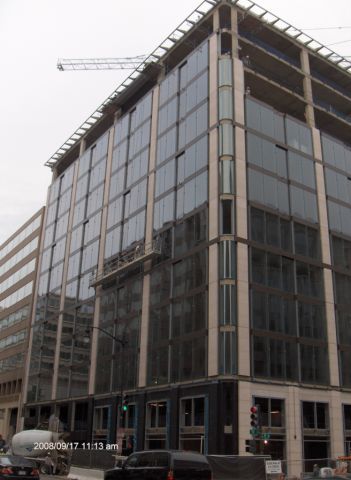 |
The Office Tower |
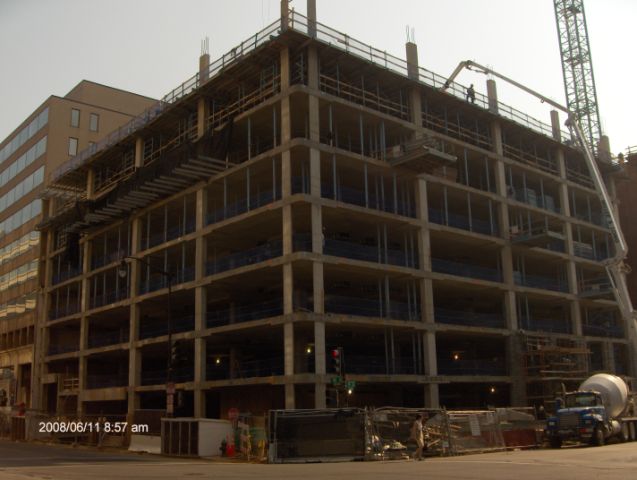 |
The Office Tower |
|
|

|
|